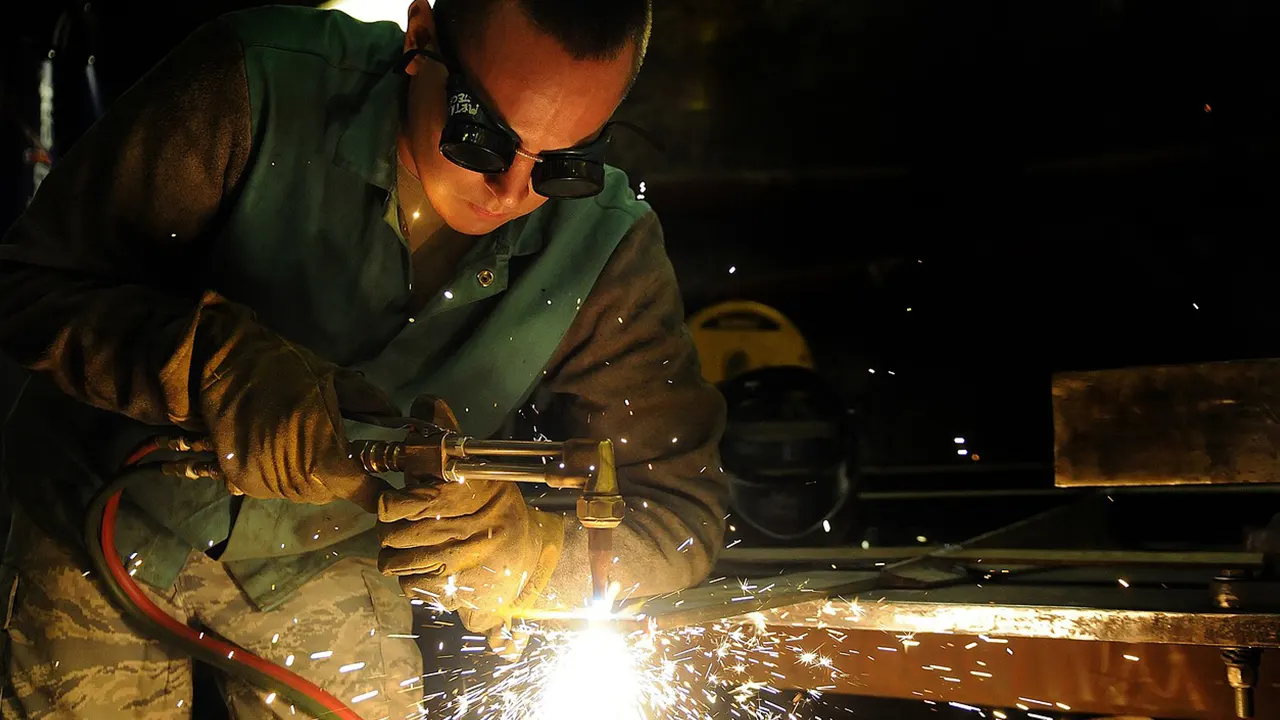
What is TIG Welding?
When compared to the three most prevalent welding methods, TIG welding is the most difficult and difficult to learn out of the three. Exactly what does TIG welding entail, then? What is meant by the term "TIG welding" is "tungsten inert gas welding."Tungsten electrodes are used in this technique, as the name of the procedure implies.
The TIG welding technique is more challenging to master, but it produces more accurate results than the MIG welding technique. TIG is also superior for connecting thinner materials and may be used to weld a variety of materials, including titanium, steel, copper, and aluminum, among others.
As a result, TIG welding is used in a broad variety of applications that demand accuracy, including those in the aerospace industry, the racing industry, industrial structures, production line manufacturing, and other fields.
1. Weld Strength
Joins that are generated by TIG welding are often more robust than those that are caused by MIG welding. This is due to the fact that TIG welding machine manufacturers produce an arc that is small and focussed, which allows for far greater penetration of the metal. It is also important to note that the TIG weld beads, when properly placed, have very few holes and other imperfections that have the potential to impair the weld.
2. The Speed of the Weld
Generally speaking, MIG welders are capable of providing quicker welding rates in a production environment. The reason for this is because air-cooled MIG welders have a more circular and larger arc, which allows them to disperse heat more effectively. Additionally, they automatically feed filler material into the weld pool. This makes it possible for welders to move the weld puddle more quickly and to operate for longer periods of time without overheating. When compared to MIG welding rates, TIG welders are unable to move the weld puddle as quickly or provide sufficient filler rod to match with MIG welding speeds.
4. Weld Strength
When compared to MIG welds, TIG welds often exhibit superior aspects of visual quality. TIG welds often just need a mild polishing to complete and remove any discoloration since they produce very little or no spatter during the process. TIG welded stacks of 'coins' are often considered to be the most visually beautiful weld. They may also be used to make unpainted welds (in steel or aluminum, for example) seem their finest.
In every application, the right preparation of metal for welding is essential to the production of high-quality products, the maintenance of constant levels of productivity, and the reduction of costs, particularly expenses linked to rework and downtime.
When you begin with the surface that is as clean as possible, the likelihood of achieving a strong and sound weld is significantly increased. Because of this, it is essential to equip operators with the best methods for conducting weld prep in a precise and effective manner in order to streamline the whole welding procedure.
1. Create a plan
When it comes to the preparation of welds, it is essential to have a strategy in place before beginning the process.
2. Cut, conform, and bevel
In most cases, the second phase in the process of preparing metal for welding is cutting, fitting, and beveling the base material. This step occurs after your design has been established.
3. Prepare the Surface and scrub it
Following the cutting and beveling of the material, the next step is to organize the surface in preparation for the first welding pass.
4. Select the Most Appropriate Level of Grit
There is a widespread misunderstanding that using a coarse abrasive would always result in a quicker completion of the task. Even though it is true that coarser and more aggressive abrasives may remove material more quickly, this kind of removal is not necessarily a desirable outcome.
Bottom Line
By selecting the appropriate product for welding preparation from TIG welding machine manufacturers and adhering to the best practices, you may increase the likelihood of achieving the results you need.