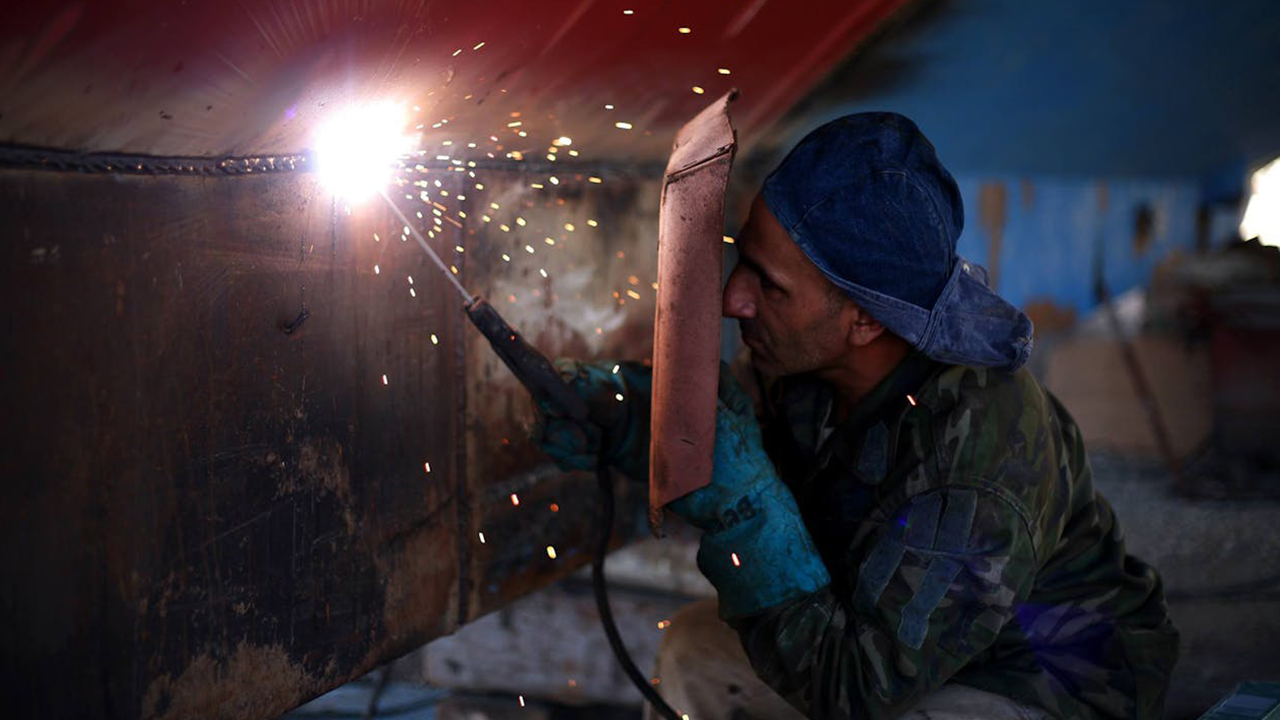
Plasma may be discovered in the natural world, it is more often discovered in the upper layers of the Earth's atmosphere. Plasma can be found in the natural world. The well-known polar lights are caused by plasma-based solar winds, which are responsible for their characteristic appearance. Plasma is an essential component of both the lighting process and the high-temperature firemaking process. And so do our bodies in the physical sense. It is estimated that it is responsible for around 99 percent of the universe that can be seen.
Plasma may be found in a variety of electronic devices, including TVs, fluorescent lights, neon signs, and, of course, plasma cutters. Plasma is something that we come into touch with on a daily basis. Through the acquisition of information about the physics and behavior of plasma, it is feasible for manufacturers to continue to improve the capabilities and efficiency of these devices. In the long run, this will lead to the development of plasma cutting technology that is not only technologically advanced but also safer.
Plasma Cutting's Fundamental Operating Concept
Once a gas is heated to an extremely high temperature, it undergoes a process that causes it to become highly ionized. This gas is referred to as plasma. This makes it possible for the power of the arc to be transmitted to the workpiece. The plasma arc cutting technique is a cutting method that includes melting the workpiece and then blowing it off, which is the situation under which the technique is able to operate well.
The compressed air is then dispersed by the gas chamber after it has been introduced into the cutting torch. This process ultimately results in the generation of plasma gas and auxiliary gas. The plasma gas arc is the one that is responsible for melting the metal, while the auxiliary gas is the one that is in charge of cooling the various components of the torch and giving a blowoff of the molten metal.
Characteristics Of The Machine That Used Plasma Cutting
1. The plasma welding cutting machines, which makes use of a number of different working gases, is able to cut a broad range of metals that are difficult to cut with oxygen. This is especially in the case of non-ferrous metals like stainless steel, carbon steel, aluminum, copper, titanium, and nickel. The cutting thickness is not altered, which leads in a larger cutting impact. This is one of the key benefits of this product. Especially when it comes to cutting sheets of regular carbon steel, plasma cutting is a process that is especially useful for cutting large metals. Plasma cutting has the potential to achieve a velocity that is five to six times higher than that of oxygen cutting. Additionally, the cutting surface is entirely smooth, thermal distortion is low, and there is almost no heat-affected region.
2. Plasma arcs may be powered by a variety of gases, including argon, nitrogen, and others. In the event that a plasma cutting welding machine is unable to successfully cut or weld thin materials, the equipment will provide results that are imprecise and inconsistent. This serves as an illustration of a thorough counterexample that is associated with the machine that is capable of plasma cutting; hence, it is essential to choose the most reputable manufacturers of plasma cutting welding machines.
3. The machine is able to automatically sort a huge number of drawings and acquire the best possible combination while it is engaged in the process of cutting them. This makes it feasible for the machine to cut all of the designs in the shortest period of time that is technically achievable.
Therefore, when it comes to tasks that include metalworking, making an investment in welding equipment that utilizes plasma cutting has the potential to dramatically enhance both productivity and quality.